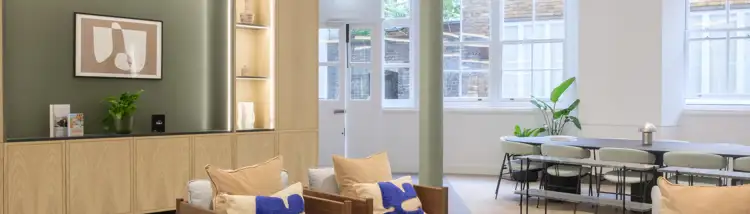
- News
Partnership Ingrained: How Early Collaboration Shaped Bloomsbury Quarter's Success
Integrated approach to complete fire door specification and delivery demonstrates significant cost and time savings


Published 09 May 2025
Most fire door projects begin with a specification landing on our desk. By then, decisions have been made, timelines are locked in, and our job is simply to deliver what's been designed. But what if there's a better way?
At Bloomsbury Quarter, we had the chance to prove that early conversations change everything. Working with Pace Interiors and 3V Architectural Hardware on this prestigious commercial development designed by Hale Brown Architects, we discovered what happens when manufacturers get involved before the ink dries on the drawings.
The Challenge: When Specifications and Reality Don't Match
Every manufacturer knows the story. A beautifully designed specification arrives that looks perfect on paper but creates headaches in practice. The door style doesn't suit the fire rating requirements. The chosen ironmongery conflicts with the frame design. The installation sequence clashes with the fit-out programme.
These mismatches aren't anyone's fault – they're inevitable when complex systems are designed in isolation. Fire doors aren't just doors; they're engineered systems where every component must work in harmony to deliver safety, performance, and aesthetics.
The industry recognises this challenge. Research shows that 85% of construction projects experience cost overruns, with design changes contributing to 56.5% of these increases. For fire doors, late changes often mean starting from scratch.
A Fresh Conversation: Design, Don't Just Deliver
At Bloomsbury Quarter, Pace Interiors invited us into the conversation from day one. Instead of receiving a finished specification, we sat down with the entire team to understand what success looked like for everyone involved.
The architect had a clear vision for how the doors should look and feel within the space. Pace Interiors needed a installation sequence that worked with their fit-out programme. 3V Architectural Hardware brought expertise on ironmongery selection that would meet both aesthetic and performance requirements.
Our role wasn't just to quote on what had been specified – it was to help design a solution that delivered on everyone's objectives whilst meeting all regulatory requirements.
This collaborative approach meant we could flag potential issues before they became problems. When we spotted that the preferred door style would require modifications to achieve the specified fire rating, we worked together to find alternatives that maintained the design intent. When the installation sequence needed adjusting to accommodate other trades, we redesigned our delivery programme to match.
What This Delivered
The results spoke for themselves. The project delivered on time and within budget, with every fire door achieving first-time compliance and matching the architectural vision exactly.
But the real success wasn't just avoiding problems – it was creating solutions that none of us could have developed in isolation. The final specification was better than anything we could have achieved working separately.
For the client, this translated into complete confidence in their fire door package. No last-minute surprises, no compliance concerns, no budget overruns. Just beautifully crafted timber fire doors that worked exactly as intended.
Making Collaboration Work
Bloomsbury Quarter proved that early collaboration isn't just nice to have – it's essential for delivering exceptional results. The key principles include starting with outcomes rather than specifications, embracing shared expertise from all team members, and designing for reality by considering manufacturing constraints and installation sequences from the beginning.
These aren't revolutionary concepts, but they require ongoing conversation between all stakeholders rather than linear handoffs between disciplines.